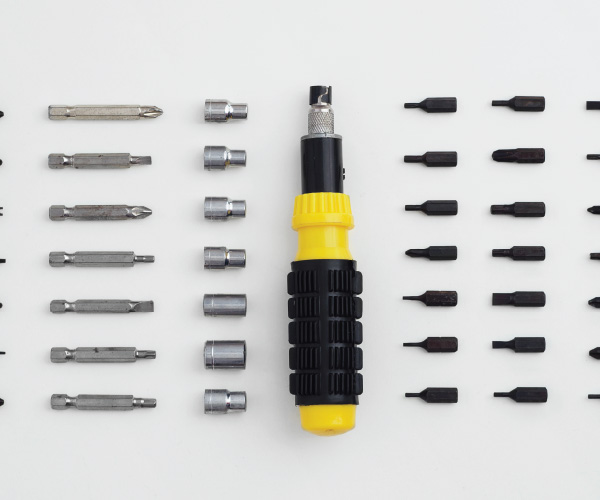
Maintenance Mastery
Using technology to manage equipment maintenance
June 5, 2023
6 minute ReadBy Tom Gresham
As the ice storm heads out, leaving behind a grey pall in the sky and on the streets — and on every car that felt its touch — a line begins to form at the car wash. Hundreds of cars with paint a shade of mottled grey and undercarriages encrusted in salt. The sensors are working at maximum speed, the brushes barely coming to a stop before starting up again, the water, dirt, salt and cleaning chemicals hanging in the air and touching every exposed surface, again and again.
It's a normal day at the car wash and indicative of what the equipment was designed to handle. “Car wash tunnels are harsh environments, which means they need reliable, sound equipment that can withstand that environment,” said Nick Haase, co-founder of MaintainX.
But, these tough, demanding conditions can make it difficult to maintain equipment and monitor its condition on an ongoing, effective basis. Unexpected failures and deteriorating performance can be costly to operators and frustrating to customers.
Technology and increasingly sophisticated equipment, however, have given operators an array of powerful tools to use to manage the maintenance and repair of their equipment — and have made that equipment more durable and reliable. Whether it is preventive maintenance or reacting to a sudden failure, technology has changed car wash owners’ and operators’ relationship with their equipment.
How software can enhance preventive maintenance
Experts agree that a preventive maintenance program is essential to extending the life of equipment and keeping it running at its best and, today, operators are investing in a range of tech-based tools to help guide their preventive maintenance efforts. ICA member Ted Yamin Jr., director of sales for Gallop Brush Co., said tech-based solutions can help keep operators on schedule and aware of possible challenges. While, ICA member Cheryl Ehmen, owner of Aerodry Systems, said software today can help keep operators organized.
“Many software options are available to consolidate the (preventative maintenance) with work orders, parts and procedures to extend the life of your assets,” Ehmen said.
ICA member Justin Salisbury, president of Breeze Thru Car Wash, said a maintenance management app with preventive maintenance scheduling is “mission critical” to keep tabs on the process and the state of equipment — and $100 in labor to perform preventive maintenance can save more than $1,000 in repairs down the line. “If you don't schedule time for maintenance, your equipment will schedule it for you,” Salisbury said.
Breeze Thru’s preventive maintenance program is broken down into daily, weekly, monthly, quarterly, bi-annual and annual recurrences to ensure it is maximizing the life of its equipment. Maintenance software such as the one from MaintainX, which Breeze Thru uses, allows operators to incorporate images, video, documents and other assets to support the techs when they are doing routine maintenance to ensure they are guided correctly when caring for the machines. Operators can attach standard operating procedures to any work order, giving techs access to step-by-step guidance on proper maintenance procedures — improving first-time repair rates and boosting team efficiency, according to Haase.
For instance, when an operator creates a work order in the MaintainX app, they can assign a maintenance task to the right tech or team and include all the details needed to get the job done.
“Let’s say a routine lubrication is required,” Haase said. “The assigned work order can include an image of the conveyor and the gears in need of lubrication. It can also contain a list of parts associated with that asset, their location, instructions and a standard operating procedure. Or, let’s say an operator discovers an equipment issue while performing a routine safety inspection. If operators don’t have an easy way to describe the issue, they mark the inspection as flagged or failed, but don't offer much detail as to why.”
With software such as MaintainX, however, users can capture photos and videos and attach them to their digital inspections, “making it easy to provide audio and visual context on the issues at hand,” Haase said.
“Compared to printed checklists or an ad-hoc text, this saves your team time in back and forth, miscommunications and seeking missed information,” Haase said. “It also simplifies the transfer of knowledge — even your newest tech will work more efficiently when they have all the information they need directly on their phone.”
Software also allows operators to track equipment, inventory, critical parts and to schedule preventive maintenance in a centralized system. Breeze-Thru also uses MaintainX to track trends in equipment breakdowns by monitoring the frequency of reactive work orders performed on different asset types. That information helps them plan and make sure critical parts are always in stock.
“Technology, when embraced with a fluid user interface, is a very resourceful tool to make equipment last longer,” Salisbury said.
Use tech to track equipment data
Technology, including software, helps operators understand and track the condition of their equipment, too.
“When you’ve implemented a maintenance management software, you can easily get the data you need to predict the health and lifespan of a piece of equipment,” Haase said. “For example, if you’ve connected a meter to your CMMS (computerized maintenance management system), you’ll notice when operating temperatures or vibration tolerances are outside a determined threshold. This can trigger a corrective action and alert your team before it impacts your operations. When you assess trends in your work orders, you may notice a spike in the frequency of reactive repairs made on a dryer or motor. … Taking these precautions will allow you to make a replacement before there’s a critical failure, tripped (variable frequency drive) or overload.”
Richard Hatcher, national sales manager, Fuji Electric, said a key to extending the life of car wash mechanical equipment — “anything driven by motors,” he said — is to use variable frequency drives. The drives allow operators to run motors at a reduced speed, and “wear on rotating equipment is a logarithmic function of speed,” Hatcher said.
“Doubling the speed of equipment does not double the wear, it increases by a much larger amount,” Hatcher said. “By operating at the lowest necessary speed, the amount of wear is reduced.”
In addition, Hatcher said, when motors are started and go from zero speed to full speed almost instantly, it causes strain on mechanical equipment such as pump couplings, the pumps and the piping with water hammer, limiting their lifespans. A variable frequency drive ramps up the speed more deliberately over a user-selected time frame, greatly reducing the strain.
Hatcher said the technology of variable frequency drives has grown more sophisticated and strengthened their importance.
“Advances in firmware and software allow much more predictive and diagnostic data to be collected,” Hatcher said. “As an example, monitoring torque loads on a conveyor belt over time could help the user determine bearing wear or other wear components that would trend upward over time, showing the upcoming need for maintenance, rather than waiting for failure or breakage.”
Innovation and changing equipment
Operators know that equipment is forever evolving, and it takes work to keep up with the latest developments and to determine how they affect their locations. Conveyors and belts for instance, have changed.
“We have belts and over/under conveyors spanning seven different brands,” Salisbury said. “Each one has seen advancements and even setbacks, but more through engineering considerations than from technological implications.”
Innovation also brings new demands to equipment in the car wash field. For instance, Yamin said the biggest challenge Gallop and other brush manufacturers face is the evolving shapes of new vehicles and continuing to look for better ways to clean the ever-changing new car lineups. Those new vehicles require new and advanced cleaning media, Yamin said. “We get new products in the field as quickly as possible,” he said.
Many equipment providers help operators with features that flag maintenance and repair needs for their equipment for operators. For instance, Gallop incorporates wear strips into its brushes, Yamin said.
“The wear strips are visual indicators that it is time to start thinking about replacements,” he said.
As new technology is added, other technology can help operators understand its impact and gauge its usefulness, Haase said.
“With proper CMMS reporting in place, you can easily measure the impact new technological advances have on your operations,” Haase said. “Teams can measure the performance of their equipment before and after any change has been made to their equipment. This provides them with accurate and reliable benchmarks that can be used to determine whether the changes were beneficial or harmful, allowing them to take action before it turns into a potential issue.”